Jefferson Union
Resources for Your Consideration
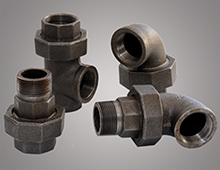
Why Do We Need Iron Seat Unions AND Brass Seat Unions?
Often a Brass-to-Iron union works well in many situations. As the iron fitting is attached, the softer brass insert conforms tightly to the iron, making a strong union. However, in many instances brass seated unions cannot be satisfactorily used on lines where the liquid to be carried has an injurious effect on the brass insert. That is where Iron Seat Unions can be used.
Inherently simple in design, Iron-to-Iron Seat Unions, with individually lapped seats, are ordinarily more trouble-free than Brass-to-Iron or Brass-to-Brass or Gasket Seat Unions. The only exception to this rule occurs on water or steam lines which must be in service without disconnecting over considerable periods of time, and then must be readily disconnected and the same union re-assembled.
Under other conditions, Iron-to-Iron Seat Unions are highly recommended as giving superior satisfaction. They should always be used where the material being carried is injurious to brass.
Since chemical solutions are apt to contain impurities, blanket recommendations should only be used as a guide; but, subject to individual conditions, Iron-to-Iron Seat Unions are particularly suggested for the following:
• Air
• Alkalies
• Mercuric Substances
• Caustic Solutions
• Copper Solutions
• Asphalt
• All Forms of Ammonnia
• Sulfate Liquors
• Chlorines (Wet)
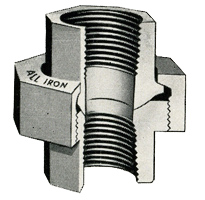
10 Reason Why Jefferson Iron-to-Iron Seat Unions Outperform All Others.
1. Union parts are machined from Air Furnace Malleable Iron castings meeting ASTM Designation A-47, Grades 32010 or 35018.
2. Female, as well as male, seating surfaces are true spherical segments maintaining seating contact throughout the entire area of the female seat.
3. Prior to assembly male and female seat pipe-ends are paired, and seats are lapped together with an abrasive paste.
4. All parts are subject to five inspection processes, including 100 lb. air test for porosity under water.
5. All unions are laboratory tested and are manufactured in the United States of America.
6. Jefferson "J" series are designed to carry ratings of 2000 PSI Non-shock COLD W.O.G. in sizes 1/8 - 2" and of 1000 PSI No-shock COLD W.O.G. in sizes 2-1/2", 3" and 4".
7. Jefferson "J" series are designed with a 15º angle back of the external tail-piece flange and the mating surface of the internal nut flange to insure full seating on pipe lines which are misaligned as much as 4%.
8. Jefferson "J" series are designed with up to 20% longer wrench-holds on pipe-ends to facilitate assembly.
9. Jefferson "J" series are designed with a basic seating angle of 30º rather than the ordinary 45º to facilitate assembly where piping freeways are limited.
10. All Unions manufactured by Jefferson have the fully chamfered pipe-ends, fully machined internal surfaces, octagonally shaped parts, clean, correctly formed and gaged N.P.T. threads to be expected of every serviceable Pipe Union.
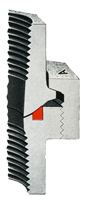
Why Jefferson Brass-to-Iron Unions are Superior
1. The castings are of the very finest air-refined malleable iron made under rigidly controlled specifications from our own patterns. Although more expensive, air-refined iron is 30% stronger than the usual cupola iron and offers 20% more resistance to distortion. Further, our patterns are so designed as to give you even more strength than found in other 300 lb. unions. Although marked 300 lb., we can conservatively recommend them for 500 lbs. — and more — S.W.P. in most sizes.
2. Brass is used in the seat for its hardness against copper; and only brass of an analysis especially developed for the job is used. We depend on true machining and precision grinding to produce leak-free unions — not a jam joint. The ring is cut from seamless tubing, giving finish on all sides and uniform density. There are no blow-holes, pin-holes, shrink spots or other ailments common to cast rings.
3. Most unions have cast channel which at best gives only a relatively smooth surface and frequently causes the seat ring to rock. Unlike them, for many years past we have been machining the channel to give a bed of precision-like smoothness for the ring so it never can sag or bulge. This makes for leak-proof tightness without having to exert undue pressure when making up.
4. The brass seating is a patented feature of all Jefferson Unions and is located in a recess away from the runway of the fitting. This prevents the ring from being loosened by the difference in the expansion and contraction of the iron and the brass and also from being dislodged, no matter how far the pipe may be screwed into the fitting. In manufacturing, the brass ring is forced into the recess so as to become practically one piece with the iron.
5. Jefferson Unions have a real ball joint with seating surfaces of a true arc carefully machined and ground together in pairs to make them absolutely tight and self-seating. The sphere of which the arc is a part is unusually large to permit the union to be sprung in more easily in cramped quarters.
6. Jefferson Unions are threaded with American Standard Taper Threads and have full length of thread, thus assuring a right fit throughout the entire length.
7. Long pipe ends permit easy installation, and all parts have square corners to help eliminate wrench slipping. The octagon shape of all parts and the wide surfaces make it unnecessary to have an special wrench — such as a Stillson — to install. The mechanic can use any wrench for the complete job.
8. Substantial chamfer on the pipe ends makes it easy to start them, and there is ample clearance between the nut and ball shoulder to prevent binding even though the pipe may be somewhat out of line.
9. Jefferson Unions are built for years of service and can be used over and over with little danger of the seats rusting or pitting.